旋盤は旋盤という機械があれば、仕事ができるわけではありません。
工作物もいりますが、それを削る刃物(バイト)も必要です。
今回は、バイトの話ではなく、バイトの素材の話をしたいと思います。
どんな金属を削るときも、刃物の選定が必要ですが、その際に重要なのがどんな素材で出来た刃物なのかです。
その次に刃物の形、角度、などを考えます。
切削工具材料の条件
・切削温度が上昇しても硬さが低下しない。
・靭性(ねばさ)が大きい
・耐摩耗性が高い
全てを満たす材料は存在しないため、工具材料は目的に合わせて機能を選択する。
炭素工具鋼(SK)(S:スティール、K:工具)
◎主要五元素により構成される鋼
・炭素(C):硬さ、強さを増幅させる。
・ケイ素(SI):酸素を除くためのもの、強さを増加させる。
・マンガン(Mn):硫黄を除くためのもの、粘り強さを与える。
・リン(P):寒い時に鋼を脆くする。 有害
・硫黄(S):赤熱状態の時に鋼を脆くする。 有害
◎リン、硫黄は製鋼上、混入を防げないので、混入量を明記し、少量のものを高級材料として使用する。
◎200℃程度で硬度低下
◎刃物用は1~1.5%の炭素を含むものである。ドリルやタップに使用されていたが、近年はあまり使わない。
◎包丁などの家庭用、大工用等で使用される鋼
合金工具鋼(SKS)(SKD) (SK、S:スペシャル)(SK、D:ダイキャスト)
◎炭素工具鋼にクロム(Cr)、タングステン(W)、ニッケル(Ni)を加えたもの
・クロム(Cr):耐食性を向上させる。
・タングステン(W):耐摩耗性、耐熱性を向上させる。
・ニッケル(Ni):粘り強さを向上させる。
◎300℃程度で硬度低下。
◎SKSは手作業用工具(全ノコ等)、SKDは金型材料として使用。
高速度工具鋼(SKH、ハイス) (SK、H:ハイスピード)
◎タングステン系
・主成分:炭素(C)0.8%、タングステン(W)18%、クロム(Cr)4%、バナジウム(V)1%
・主成分の数字をとって、18-4-1で表される。
◎モリブデン系
・タングステンの一部をモリブデン(Mo)に置き換えたもの Mo1%がW2%に相当する。
・モリブデン(Mo)耐摩耗性が高い。
◎現在使用されている一般的な切削工具材料では硬度が一番低い
◎600℃程度で硬度低下
◎近年、靭性を損なわず、さらに耐久性を向上させたものに粉末ハイスとコーティングハイスがある。
粉末ハイスは、粉末焼結法によって、微細炭化物を均一に分布させ、Vを多く添加できるため、耐摩耗性が向上する。
コーティングハイスは下の、PVDのこと
超硬合金
・基本型は炭化タングステン(WC)の粉末と結合剤である
W、チタン(Ti)、タンタル(Ta)、V、Mo等を粉末にし、一種又は数種を組み合わせて、コバルト(Co)、ニッケル(Ni)を焼結した焼結合金
・材料特化向上のため、炭化チタン(Tic)、炭化タンタル(Tic)等を添加したものである。
・硬度はHRC(ロックウェル硬さ)90ぐらいあり、高温硬度は1000℃で約20%硬度低下する
・材質により使用区分が分けられる
鋼切削用:P種 連続したキリコが出る工作物 切削抵抗:大 連続型切り屑
ステンレス切削用:M種 切削抵抗:中 せん断型切り屑
鋳鉄切削用:K種 断続したキリコが出る工作物 切削抵抗:小 裂断型切り屑
P種が一番粘い、K種になるにつれて、脆くなる。 M種はPとKの間
コーティング工具
◎ハイス超硬の表面に被膜を形成し、耐摩耗性や耐摩擦特性を向上させる。
CVD(科学的蒸着)
・被膜物質:TiN、TiC、TiCN(炭窒化チタン)、Al2O3(アルミナ)、SiC(炭化ケイ素)
・原理:成分元素を分子化にガス化し、化学反応によって被膜を形成する。
・膜厚:2~20μm
・特性:密着性が高く、高負荷に耐える。表面精度がPVDに劣り、膜厚が厚くなるため、刃先の丸み(ノーズR)が大きので、精密加工に向かない。
PVD(物理的蒸着)
・被膜物質:TiN(窒化チタン)TiCN、CrN(窒化クロム)、TiAIN(窒化チタンアルミニウム)、ZrN(窒化ジルコニウム)、HfN(窒化ハフニウム)
・原理:成分物質を蒸発、イオン化(分子から電子を奪う)させ、被膜を形成させる。
・膜厚:1~10μm
・特性:密着性がCVDに比べ弱く、はがれやすいため断続切削に向かな。表面精度が良く、膜厚が薄く刃先の丸みを小さくできるため、精密仕上げ加工に向いている。
サーメット(Ceramics+metal=cermet)(セラミックス+メタル=サーメット)
・当初、炭化チタン(Tic)80%でNi-Moを結合剤として焼結合金として開発された、炭化物系超硬合金の一種。
・化学的には安定しているが、熱伝導率が悪く、脆い。 チッピングをおこす。 使用制限あり。
・その後、TiCをTiN(チタンナイトライド)に置き換え、熱伝導率、靭性を向上させたものが現在の主流となっている。
欠点が改善されて、耐酸性向上。耐チッピング性、耐クレータ摩耗性にすぐれ、断続切削も可能となり、仕上げ面がきれいである。
セラミックス
・工具材料では、Al2O3(アルミナ)を主成分として、ホットプレスやHIP法で焼結して作ったもの。
・結合添加剤を含まないため,高温硬度(1500℃まで耐える)、熱的・化学的耐摩耗性に優れる。
・靭性がかなり乏しく欠けやすい。 耐熱衝撃性は超硬、サーメットに劣る。
・その後、Al2O3-TiC系(アルチック)のセラミックスは靭性を高め、鋼材、焼入れ部品の切削、断続切削を可能とした。
CBN(立方晶窒化ホウ素)
・CBNの粉末を高温、超高圧で圧縮焼結したもの。
・ダイヤモンドの次に硬い。
・主に、HRC50以上の焼入れ鋼や、耐熱合金、工具材(ハイス)等の超高度材の切削が可能。
・軟鋼切削時は、摩擦が大きくなり、刃先寿命を下げる。
・高速切削の工具材料として、高価であるが広く使われる。
ダイヤモンド
・天然ダイヤモンドと焼結ダイヤモンドがある。
・天然ダイヤモンドは全ての物質の中で最も硬く、熱伝導性、耐摩擦性に優れ、他の材料との親和性が低い。
・非常に脆く、鉄に反応し易く、高価である。
・非鉄金属の高速精密切削加工に使用される。
・高速切削時の微小送り加工では、精密で表面品位のよい仕上げ面が得られ、銅、アルミ、真鍮などの非金属の加工に使用され、超精密切削工具として普及している。
・人造ダイヤモンドは超高圧高温技術によって、超硬合金の基盤の上に、緻密に焼き固めたもの。鉄系材料に反応しやすく、大気中で高温になると炭化するため、非鉄金属を中心に利用されている。
硬さ、ねばさ。
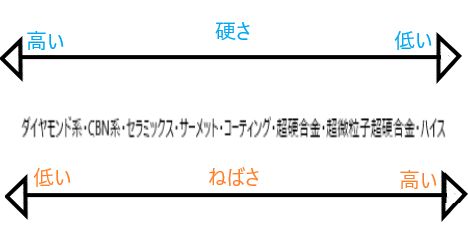
はじめに書いた、切削工具材料の条件で硬さとねばさがありました。
硬さとねばさは両立しないので、条件によって刃物選定が重要になってきます。
皆さんは何を使っていますか?
自分は、サーメット、超硬、コーティング、たまにハイス、かな?
ドリルやタップはハイスかな
実際に働いている方で、自分が使っている刃物素材が、わからないでいる方もおられるかと思います。
先輩の言う通りで動いている人です。
今度からは、素材も考えてみて、旋盤作業の理解度を深めていきましょう!
自分もまだまだです。
理解度や技術度を深め、高めて行かなければなりません。
これからも切削工具は多種多様化していきます。素材の特性を把握した上で、選択眼を養っていく必要があると思います。
お互いがんばりましょう!